Jones + Attwood™ Jeta® Grit Trap
Grit removal is a prerequisite of wastewater treatment. It prevents buildup in process chambers, and erosion of equipment in the primary treatment works. The Jeta Grit Trap is a high performance, efficient and compact grit removal unit.
With its sloping sides and specially designed impeller, the Jeta Grit Trap provides maximum separation of heavy mineral solids (grit) while rejecting lighter organic solids. This system provides the highest possible grit removal performance in a small plan area.
Grit removal is a prerequisite of any wastewater treatment plant before it enters the next phases of treatment. If not removed at the beginning of the treatment process, grit will settle and harden downstream, such as in the activated sludge tanks, resulting in a reduction of the available volume/residence time. Unremoved grit can also impact downstream equipment, such as pumps, that would face increased wear as well as potential sludge handling hurdles.
The Jeta Grit has been thoroughly engineered as a compact, efficient system that is economical due to lower excavation and civil works costs for new installations. Ovivo achieves this by incorporating readily available, precast concrete rings in the design, or for retro-fitting the mechanisms into existing plants. This system is an established technology for grit removal, with over one thousand installations worldwide.
The Jeta Grit has the following features and benefits:
- The fully automatic, low head loss system consumes less energy than competitive devices and is sized to suit plant flow requirements
- No submerged contact points, maintenance is reduced and easier
- Our compact design offers a reduced footprint
Downloadable Resources
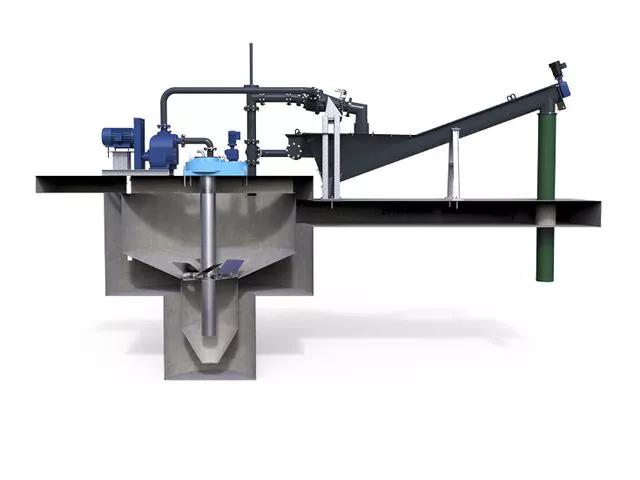
Municipal grit generally has attached fats, oils and greases or other matter that may includes inorganic food waste, bones, road tar, bits of metal and sticks. This changes the specific gravity from the ideal 2.65 of “clean” grit, making it more complex to process.
Wastewater enters tangentially, flows around the system’s tank, and exits parallel to the inlet. Two positive zones are set up within the grit trap chamber. The outer chamber is quiescent, and thus allows the grit to settle on the inclined floor of the chamber. The impeller’s predetermined speed produces radial forces that allow the grit to fall into the collection hopper. These forces also act on the lighter solids preventing them from entering the hopper. The lighter solids are retained in the water flow and carried out of the grit trap for processing in downstream. This results in much cleaner grit by preventing the organics from dropping into the grit hopper. The grit is moved to washing, classification and dewatering equipment, using a pump system.
Grit remains in the system until it is transported to the wastewater treatment plant. The first flush significantly increases the grit load, from 10 to 30 times on average, due to much higher flow velocities. Grit that is not removed at the head works will accumulate at every opportunity and harden to a concrete like material. Grit volume generally has the range 0.53-5.0 ft3/MGD in most wastewater treatment plants. The preferred method for grit removal is using a top mounted, self-priming grit pump. Mounting the grit pump on top of the grit trap simplifies the civil works and allows easy access for maintenance of the pump.
REMOVAL EFFICIENCY:
- 95 percent removal of grit larger than 50 mesh
- 85 percent removal of grit larger than 70 mesh but less than 50 mesh
- 75 percent removal of grit larger than 100 mesh but less than 70 mesh
HEAD LOSS:
- Less than 1/4 in at peak design flow
DESIGN OPTIONS:
- Original 270 design or the 360 design is available for all sizes